Advancing sustainable construction
As the world becomes more urban, the demand for sustainable construction solutions is at an all-time high. We need to rethink production methods and decarbonize manufacturing to reduce environmental impact and shape a more sustainable built environment.
Geocycle’s solutions transform waste into resources to decarbonize the cement manufacturing process, preserve natural resources and create a circular loop.
Decarbonizing the built environment
By 2050, around 80% of the world’s population will live in cities while 60% of the buildings that will exist by then have yet to be built.1
This demands a responsible approach to construction. The industry today produces approximately 39% of global carbon emissions and 33% of global waste.2
Sustainable construction and renovation focus on using less energy, water and materials than traditional methods to generate less waste and carbon emissions.
Geocycle’s solution contributes to decarbonizing the production of building materials to enable more sustainable construction.
1 World Economic Forum
2 World Green Building Council
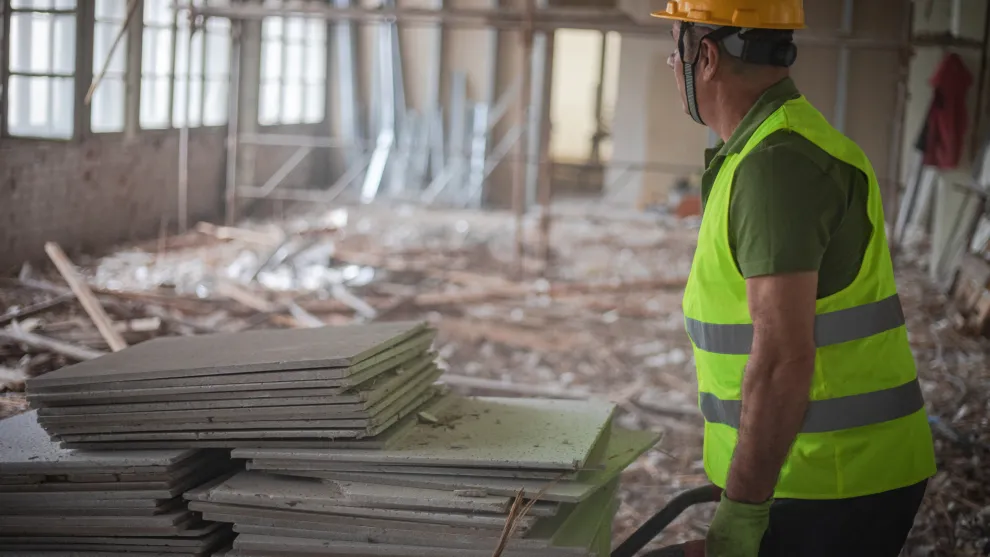
Enabling more sustainable building materials
Geocycle provides the expertise to recycle raw materials as inputs for cement production to make construction more sustainable.
We provide a low-cost solution for waste management and sustainable construction by using existing cement infrastructure. This reduces the need for further investment in dedicated facilities.
During the cement-making process, we replace carbon-intensive traditional materials and fossil fuels with low-carbon equivalents, such as waste biomass, to reduce CO2 emissions.
Recycling end-of-life materials enables us to reduce the use of virgin resources in construction projects. In this way, we continue to close the circular loop and preserve natural resources.
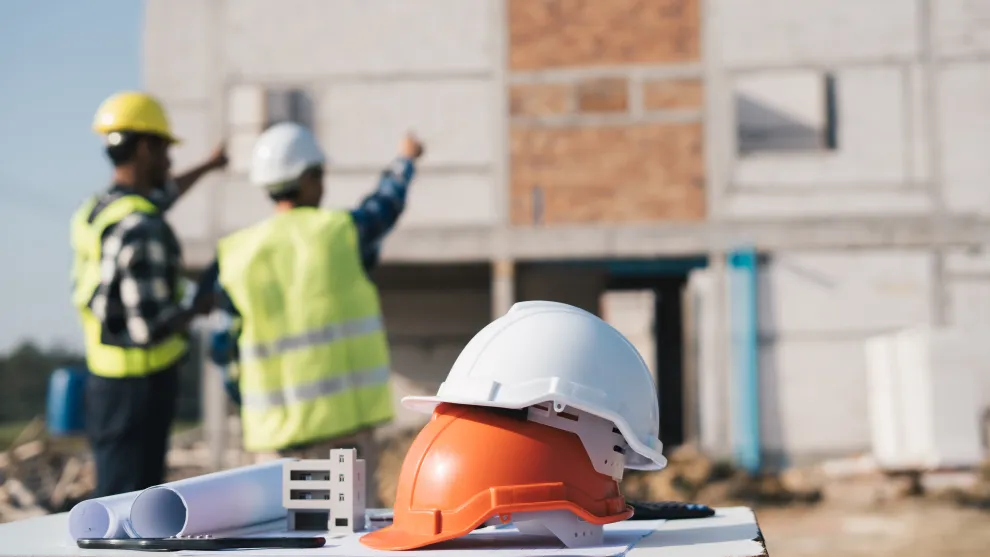
How do our solutions work?
At Geocycle we transform waste through pre-treatment and co-processing. Pre-treatment requires considerable expertise and investment. It involves turning a wide variety of waste into a homogenous mix through shredding, blending and drying.
Once materials are suitable for the cement kilns, the next step is co-processing. This method recovers energy and materials from waste to power the cement production process, substituting clinker – the principal ingredient in cement that is highly energy intensive to produce.
As a result, 100% of the waste input is recycled and recovered without producing any residue.